Project summary
Project title
Informed Finite Element Modelling for Wire and Arc Additively Manufactured Metallics — A Case Study on Modular Building Connections
Project lead
Northumbria University
The use of 3D printing in modular building connections is a novel and promising technique. However, the performance of 3D printed steel modular building connections has not been investigated adequately to date.
A three-dimensional finite element model (FEM) has been developed, using the multi-purpose software Abaqus, to study the effect of different geometrical and material parameters on the ultimate behaviour of modular building connections (herein named 3DMBC) using a wire and arc additive manufacturing (WAAM) method, as part of the UK’s 3DMBC (3D Modular Building Connections) project.
The proposed model considers material and geometrical nonlinearities, initial imperfections, and the contact between adjacent surfaces.
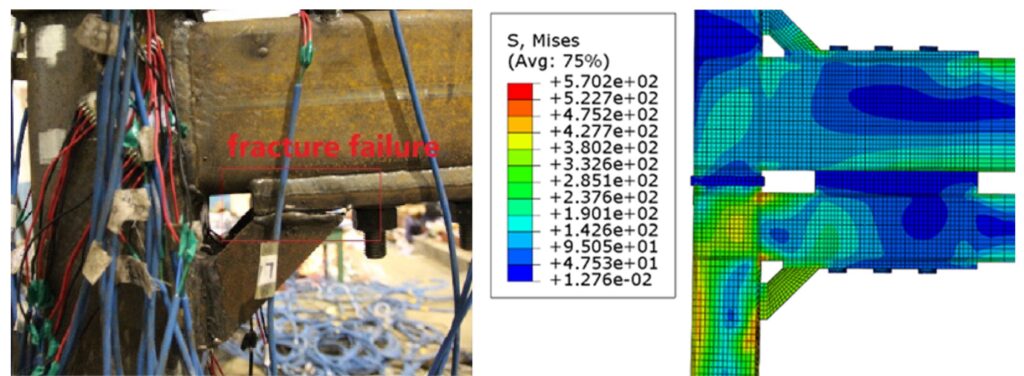
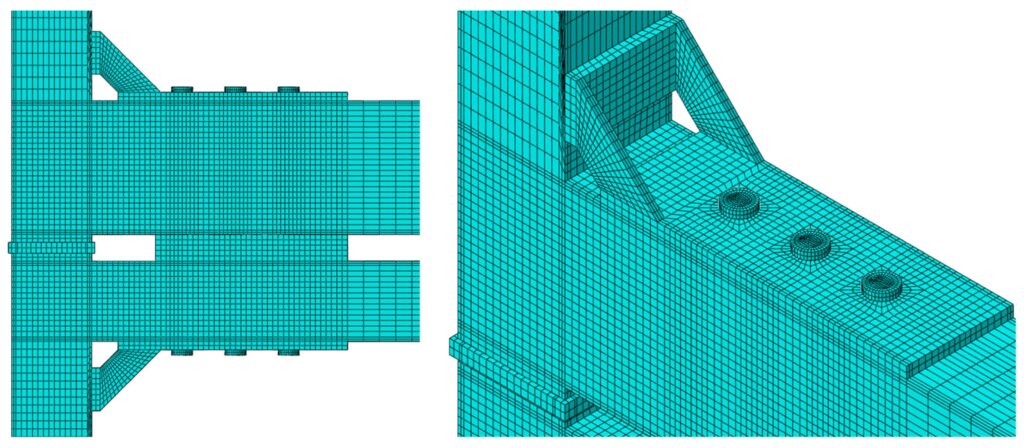